Let us go back to the widget example. Your project is in production, and you want to know if a design change would affect the product. For example, you go from having a steel handle on your widget and want to see if you can switch it to aluminum. Comparative analysis can look at both options and analyze whether the change in the design will affect the feasibility of changing out that design component.
Understanding the Importance of Stress Analysis: When to FEA and When Not To
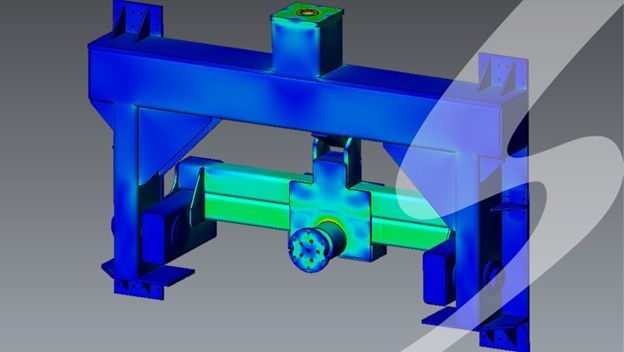
Understanding the stress, strain, and deflection in machined parts is critical to the overall success of a project and operations. It is important for engineers to understand stress analysis and the proper times to conduct a finite element analysis (FEA) and when not to. Let’s take a deeper look into the importance of stress analysis and how finite element analysis is used.
The Importance of Stress Analysis
What is stress analysis? Stress Analysis is the testing of objects against various load conditions. Engineers use stress analysis to determine the strain and stress put onto a material that is subjected to different types of force. We define stress as the force per unit of area. (S=R/A.)
As disciplined engineers, we use stress analysis to test the design of all kinds of structures from tool handles to the structure of a bridge or building. Through testing, engineers hope to discover weaknesses in the design prior to production. Stress analysis is also used for forensic analysis to determine the root cause of equipment failure.
Why would we need to do this kind of discovery testing on designs before they go into production? Simply, preventing structural failure is one of the most important jobs an engineer can have.
What is a Finite Element Analysis (FEA)
Finite element analysis (FEA) is a computer simulation used for stress analysis of solid objects. Through computer simulations, engineers can test solid objects while simulating different loads virtually.
Through FEA software, engineers can help to identify engineering and mathematical problems including structural analysis, fluid flow, heat transfer vibration analysis and fatigue analysis. By conducting FEA testing, engineers can simulate the stress put on a design before producing prototypes. It allows engineers to optimize design components prior to production.
When to Utilize Finite Element Analysis
Let’s say you have a new product we are going to refer to as a “widget.” As the inventor, you created this widget to solve a problem that you did not see a solution for. Think of the screwdriver that can be used in tight spaces or a new design for a can opener that makes opening things faster and easier. So, you want to make sure before you produce millions of these widgets that it stands up to the test of time. The last thing you want as the inventor is for the product to break the first time a consumer uses it.
Things evaluated using FEA:
· Stress
· Vibration
· Buckling
· Creep
· Heat Distribution
This is where FEA comes in handy. You take your idea to Seifert Technologies and our team of engineers uses software to create a 3D model rendering of your widget. We then would run an FEA that relates to a certain loading case to which the widget would be subjected. The team will then recommend design changes based on the analysis of the design through our FEA software. You the inventor of the widget is thrilled to have a digital proof of concept that you can then take to your manufacturer to design to specifications.
Here are some of the components useful for FEA analysis:
Linear vs Non-Linear Analysis:
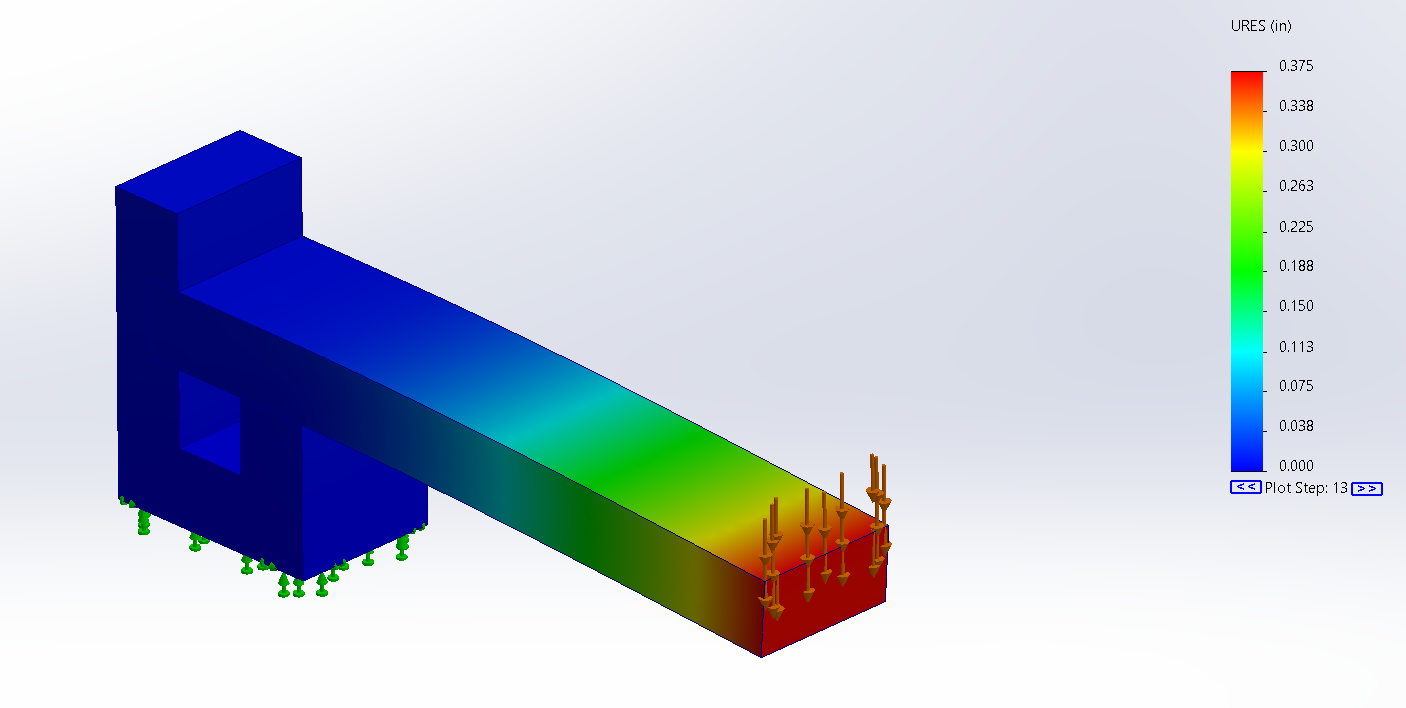
A linear static analysis is an analysis where a linear relationship remains constant between the applied forces and displacement. A non-linear analysis is where a nonlinear relationship occurs between the applied forces and the displacements. Nonlinear effects can originate from the material, contacts, or large deformations. An example of a nonlinear material would be plastic or rubber. An extremely cantilevered beam is a classic example of a nonlinear analysis due to the large deformations near the end of the beam.
Static vs Dynamic Load:
While static loads are constant, dynamic loads change over time. This is a comparison of the stress a load has on an object. Then look at a bridge for example. There is a static load that makes up the materials of the bridge and a dynamic load of environmental elements like snow, wind, water, and heat. As well as the vibration and weight of the traffic across the bridge that is constantly changing. That changing elements are part of the dynamic load of the bridge. The static load is the element that remains constant.
Comparative vs Absolute:
Understanding the Importance of Stress Analysis:
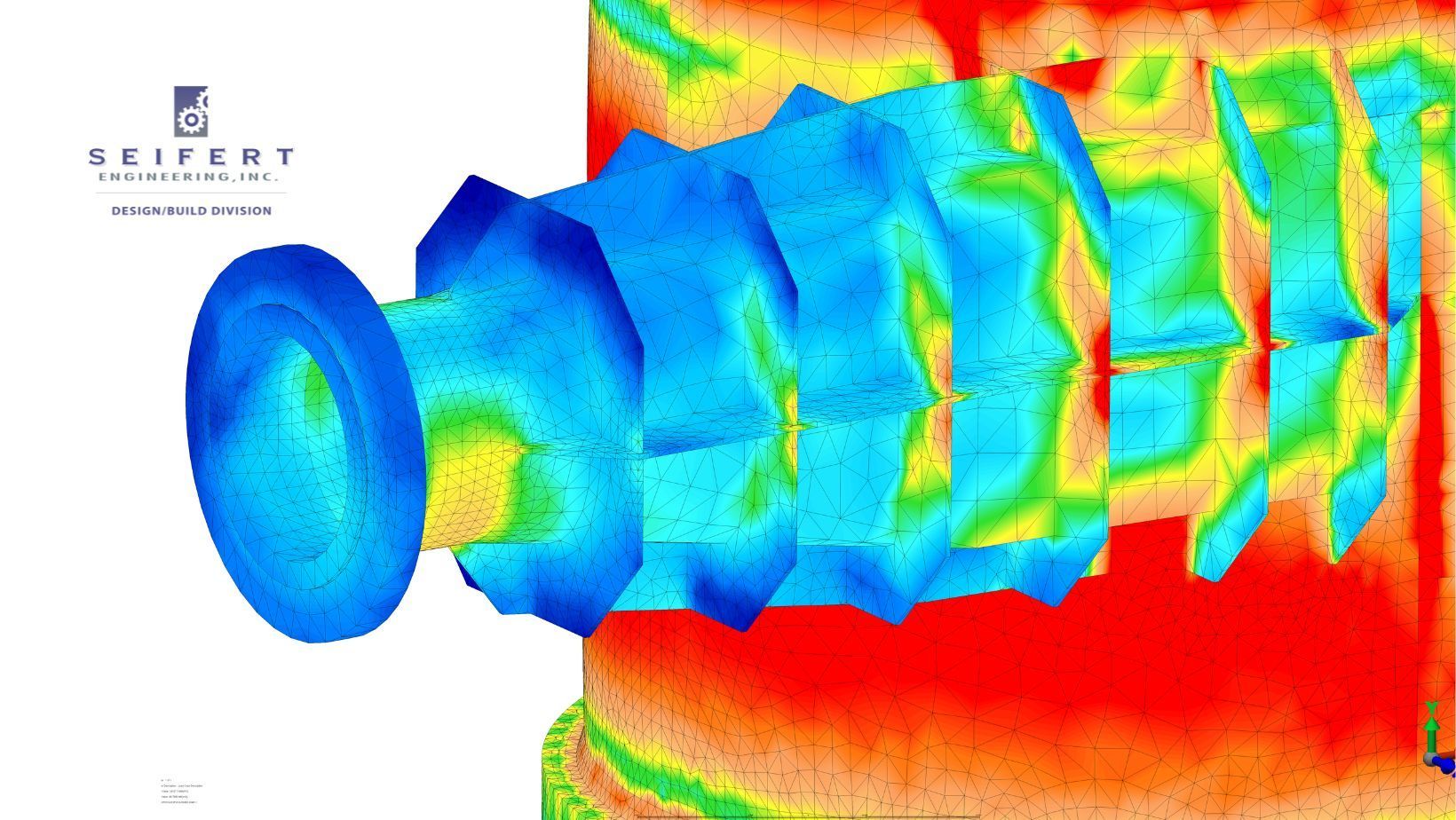
Simply conducting an FEA analysis is not enough. The design must be analyzed by engineering experts. Typically, the best FEA confirmation doesn’t just come from the primary design tool but is combined with calculations to confirm critical analysis results. The complexity of the overall assembly should be broken down into parts. For instance, you don’t do a test on a fully functioning car, but rather, you do a study on the frame design for the car model.
You need to have people with experience to analyze the results of your FEA testing. They must have good mechanical aptitude and a solid understanding of the classical solution to confirm the FEA results.
FEA analysis must be reviewed by engineers. The software alone will not give you a full picture of the potential design flaws. You must have verification and validation of a design from qualified engineers. The FEA study alone is not enough.
Conclusion
FEA design services are an essential part of product development. Using FEA to strategically identify potential issues in the initial design process can save you time and money. It is financially and ethically sound to utilize all the technology available to produce the best product on the market.
Seifert Technologies’ FEA Services allow you to create virtual prototypes of your most complicated designs. Simulating real-world conditions on your designs related to stress, temperature, and vibration allows you to bring your products to market faster with better results. This process allows you to optimize your design before fabricating the level one prototype.
If you are looking to outsource your engineering analyses, hire the professionals at Seifert Technologies. Contact us today.
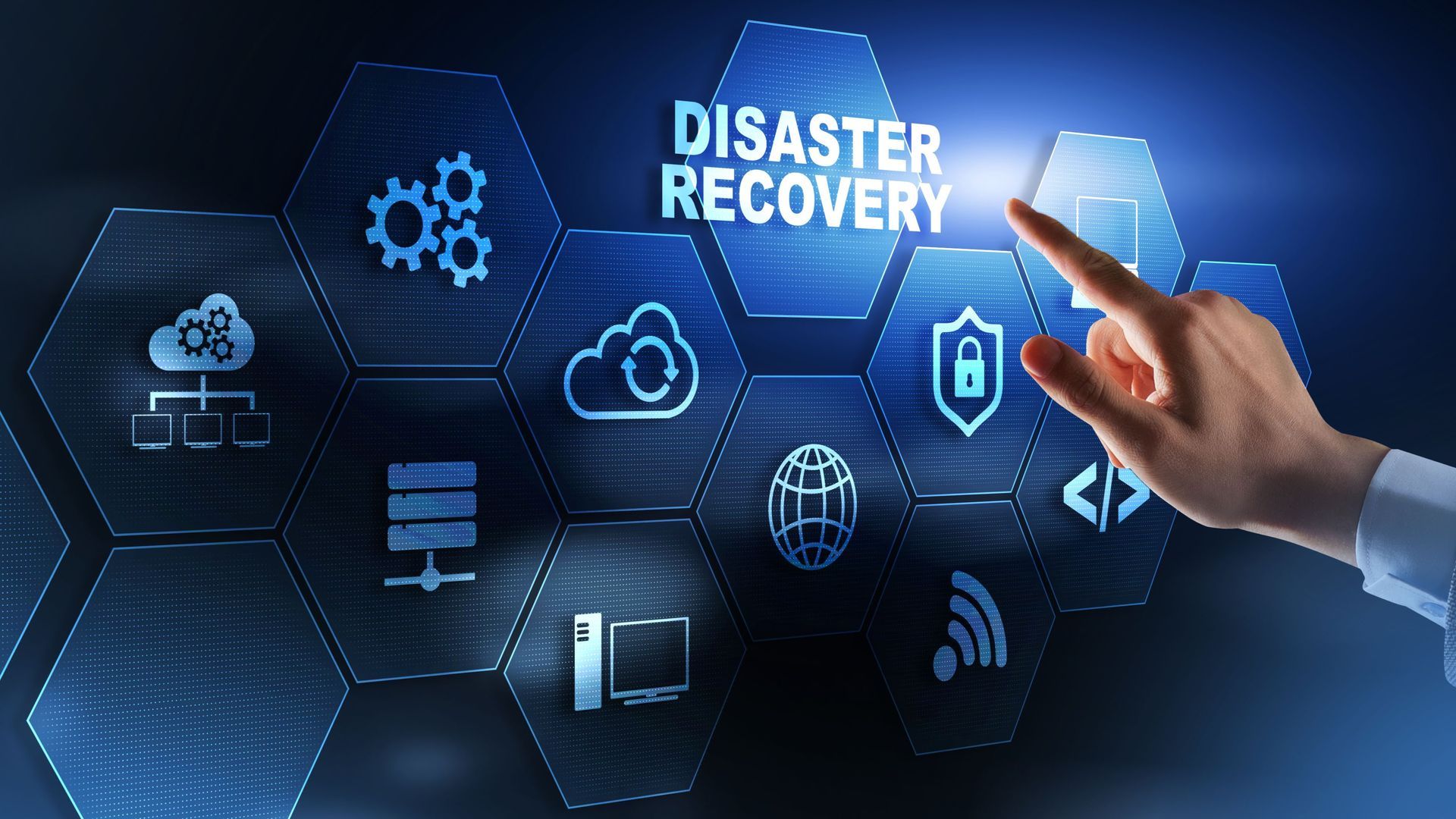
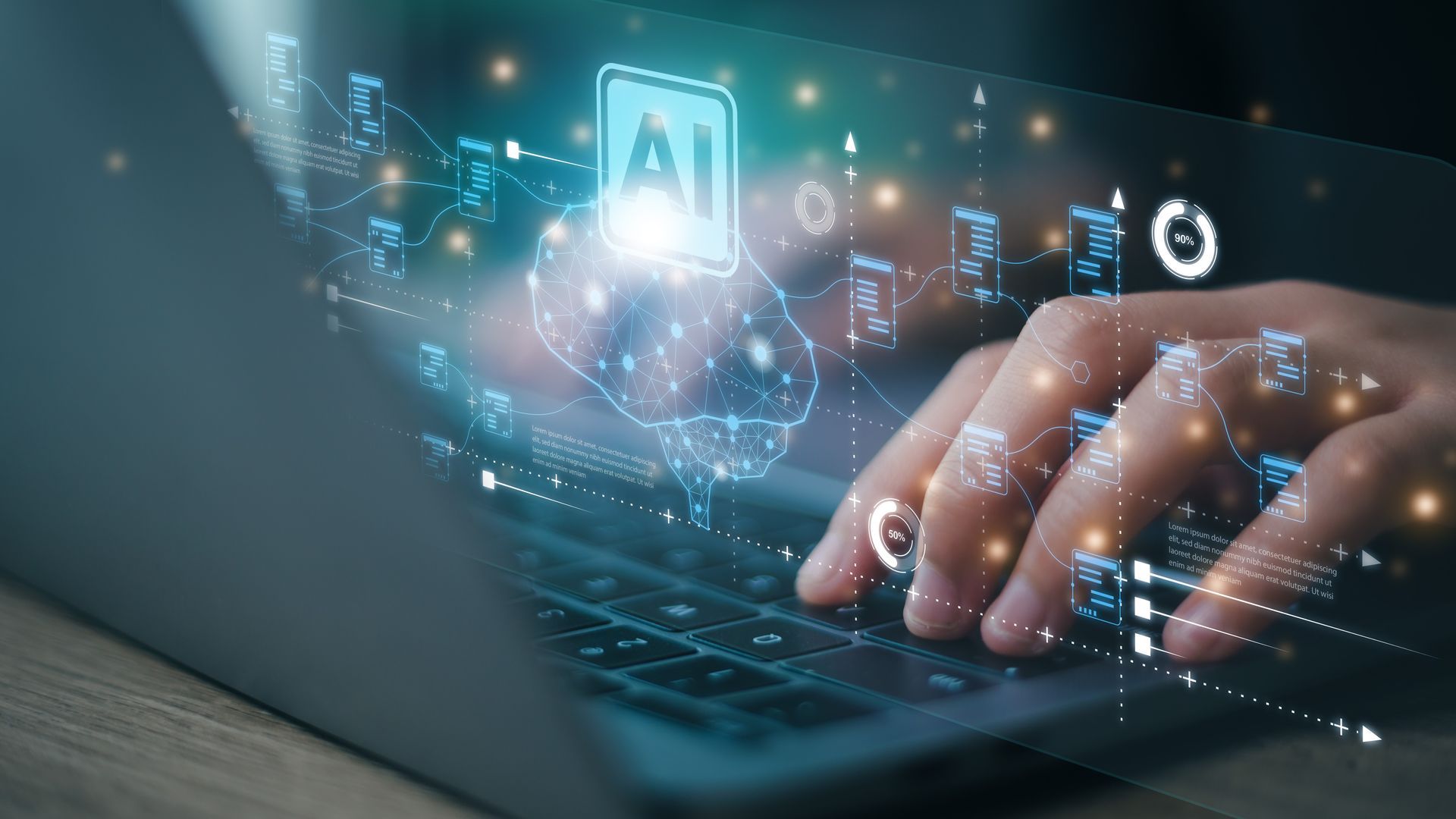
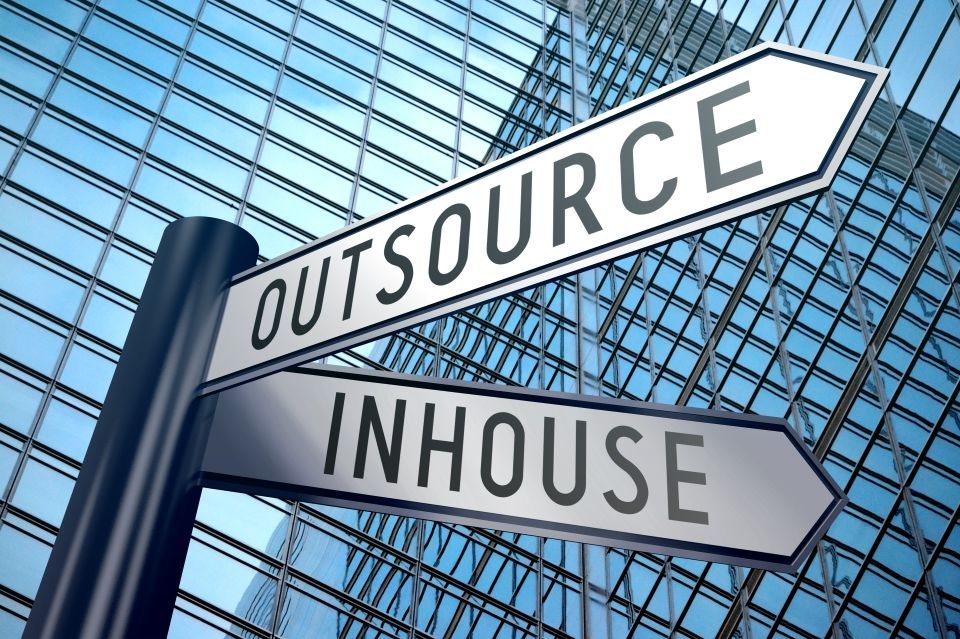
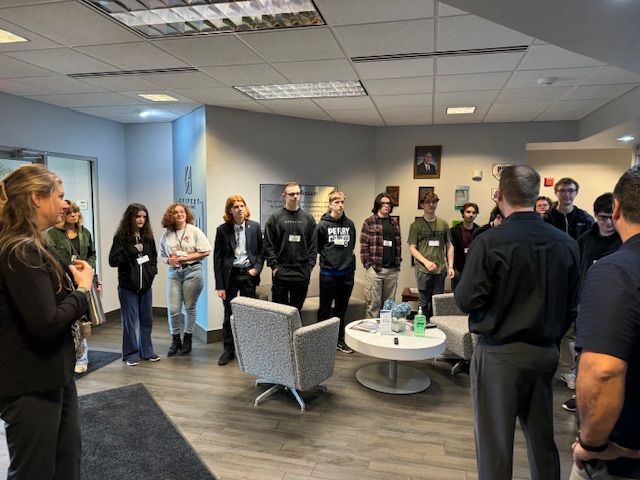
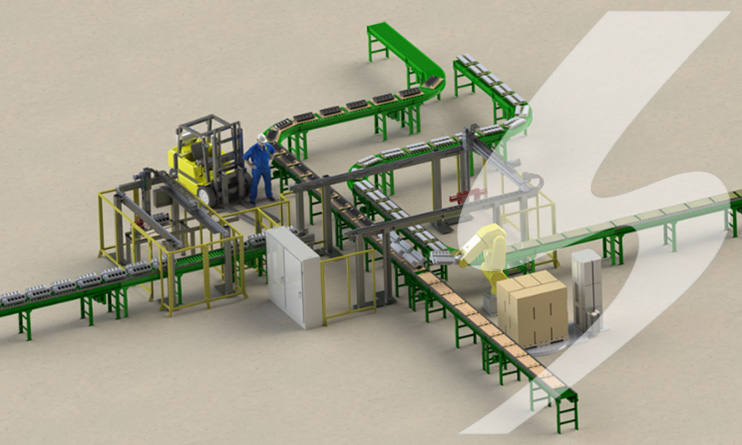
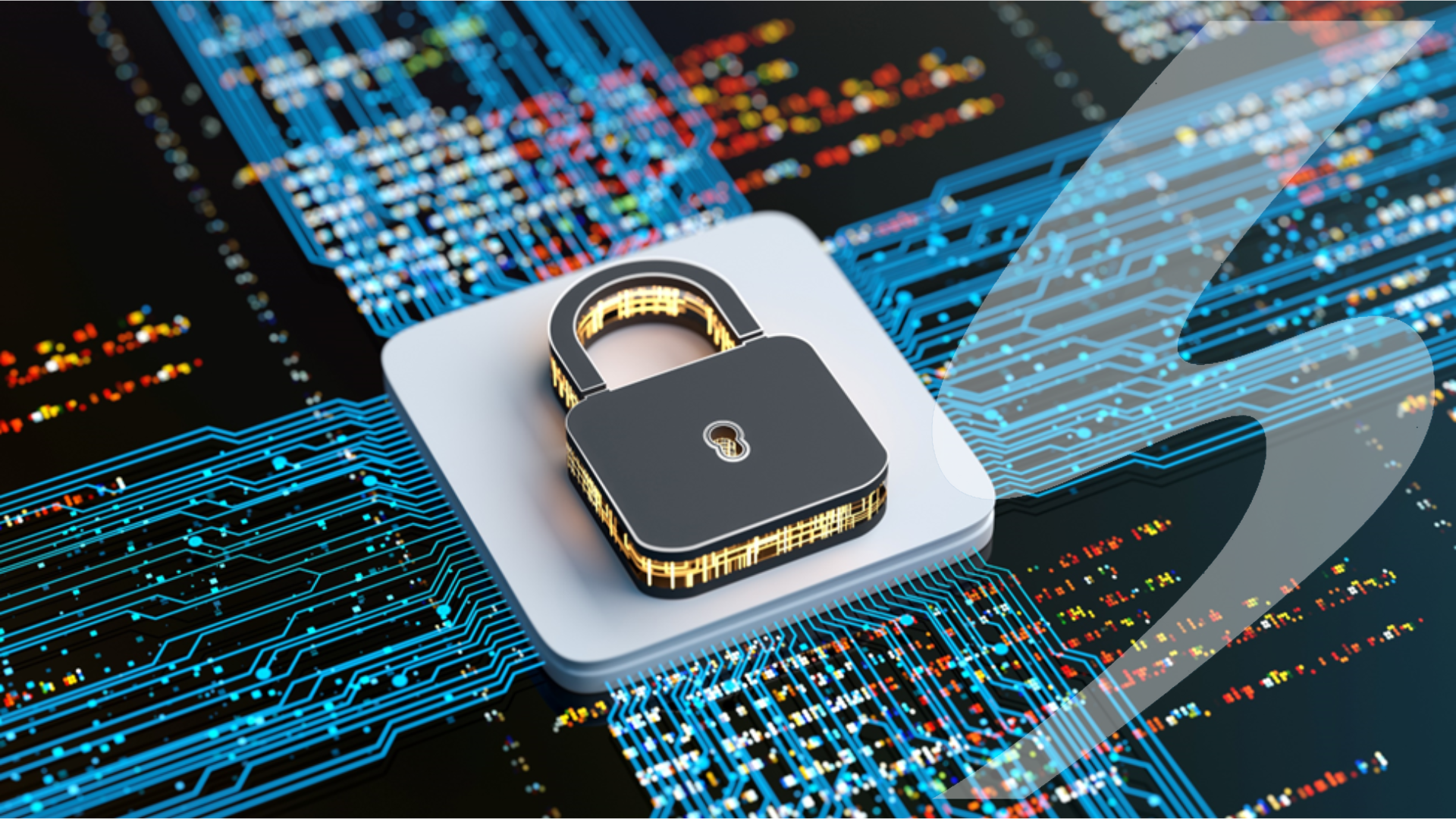